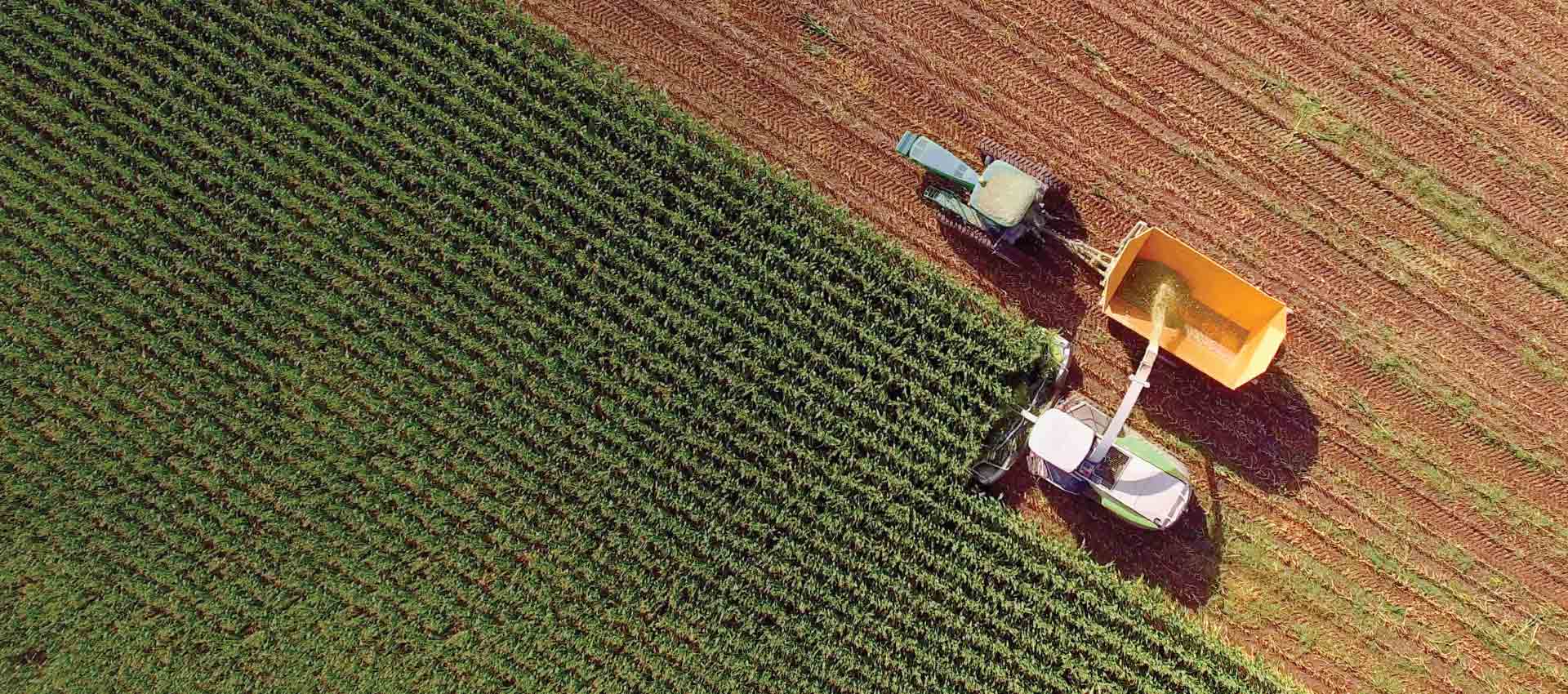
Technology Category
- Analytics & Modeling - Machine Learning
- Functional Applications - Manufacturing Execution Systems (MES)
Applicable Industries
- Education
- Food & Beverage
Applicable Functions
- Procurement
- Warehouse & Inventory Management
Use Cases
- Additive Manufacturing
- Demand Planning & Forecasting
Services
- Data Science Services
- System Integration
The Customer
Not disclosed
About The Customer
The customer is a global agribusiness and food manufacturer with over $100 billion in annual revenue in 2020. The company operates approximately 1400 manufacturing and distribution sites worldwide and employs over 150,000 people. It operates in over 120 countries and produces over 80 million pounds of food products per year across 90+ product codes and various raw materials. The company's only customer is a global retailer, and it faces significant challenges in demand forecasting and production scheduling due to the highly variable demand of this customer.
The Challenge
A global agribusiness and food manufacturer, producing over 80 million pounds of food products per year across eight production lines, faced significant challenges in demand forecasting and production scheduling. The company's only customer, a global retailer, exhibited highly variable demand, leading to discrepancies with the manufacturer's weekly demand forecast. Traditional demand forecasting solutions, based on statistical algorithms, were unable to cope with the short lead times and daily sales orders due to the short shelf life of food products. This resulted in unfulfilled customer orders. Additional rule-based solutions procured to improve production scheduling also failed to optimize schedules and significantly improve manufacturing operations.
The Solution
To address these challenges, the company decided to implement the C3 AI Demand Forecasting and C3 AI Production Schedule Optimization applications. The C3 AI team began by ingesting, cleansing, and unifying 18 different data sources, including historical demand forecasts, order history data, production history, manufacturing specifications, and historical inventory levels. This unified data image enabled the company to train and configure the AI applications. The C3 AI Production Schedule Optimization was configured to automatically generate schedules based on the latest available data, reducing the time to generate schedules by 96%. The user interface across both applications was configured to enable users to view critical manufacturing KPIs, identify KPIs at risk, evaluate and approve AI-recommendations, and develop multiple scenarios by tuning inputs into the scheduling algorithm.
Operational Impact
Quantitative Benefit
Case Study missing?
Start adding your own!
Register with your work email and create a new case study profile for your business.